Manufacturers
Track viscose manufacturers’ progress in the transition to closed-loop production.
With careful chemical management, viscose can be produced in a responsible way through a closed-loop system, whereby chemicals are captured and reused instead of being released into the environment. However, many manufacturers are yet to adopt best practices.
Our Roadmap identifies the emissions standards for viscose set out in the European Union’s Best Available Techniques (BAT) Reference Document (or BREF) on polymers1 as the most comprehensive and ambitious standard. The BREF is the result of an exchange of information, carried out from 2003–05, between EU Member States, the EU viscose industry and NGOs. It is based on operating data that EU industry players supplied at the time, meaning the values and techniques set out in the BREF reflect what the best performers in the industry were already achieving over a decade ago.
The document sets limits on chemicals usually discharged from the viscose staple fibre manufacturing process and addresses pollution to both air and water.
Table 1: EU BAT emissions standards for viscose staple fibre production
While the EU BAT does not set best practice for viscose filament yarn production, the BREF document provides emission and consumption data for viscose filament yarn production from the European Man-made Fibres Association (CIRFS), which can be used as a good reference/indication of best practice.
Table 2: Emissions and consumption data for viscose filament yarn production
The table below examines commitments and actions implemented by the world’s leading viscose manufacturers in the transition to responsible viscose – specifically, Lenzing AG, the Aditya Birla Group (ABG), members of the Chinese Collaboration for Sustainable Development of Viscose (CV initiative),2 Sateri, which is a member of the CV initiative, and ENKA.
For more specific information about manufacturers’ commitments and actions, download the Excel table.
Download tableKey:
Commitment to EU BAT
Production sites operating in line with EU BAT
Investment towards closed-loop technology
Transparent reporting on progress towards meeting EU BAT parameters
Grievance mechanism and remediation procedures
Canopy 2019 Hot Button Ranking

Lenzing required all sites to comply with the Group Environmental Standard, which is aligned with EU BAT, by 2022.1
Lenzing communicated that a delay is expected due to negative impacts by Covid19.
2 out of 3 viscose producing facilities;Lenzing Austria and Nanjing, China.
Lenzing intends to invest over €100 mn in ‘sustainable production technologies’ by 2022. Throughout 2019 and 2020 it has attributed over €3.7 mn (US$ 4.4 mn) in SPV; €40 mn to expand the production of the raw material sulfuric acid at the Lenzing, Austria site; and around €2 mn (18 Mio CNY) in Nanjing, China site to improve waste water treatment and Carbon disulfide Adsorption Plant (CAP).
Limited public disclosure, including information on reduction of certain emissions within a set timeframe on a group/facility level, but no systematic reporting of progress made by all facilities in relation to EU BAT parameters.
Lezning has a BKMS® whistleblower system, publicly available for all facilities and to all employees of the Lenzing Group, to customers, suppliers and other third parties globally. Accessible publicly via website, but not available in local languages.6
Incidents/complaints not publicly accessible. They are registered in Group's Safety, Health & Environment Action reporting system (SHEARs) followed by a root cause analysis and corresponding actions taken.
Green shirt: 30.5/35 buttons
Sourcing risk of sourcing from Ancient & Endangered Forests and other Controversial Sources has been resolved.

ABG aimed to achieve EU BAT norms at all its sites by 2022.2
ABG communicated that a delay is expected due to negative impacts by Covid19.
4 out of 7 viscose producing facilities; Birla Jingwei Fibres Company Limited (BJFCL) in China, Thai Rayon Public Co. Limited (TRC) in Thailand and Grasim Vilayat in India.
ABG committed a total of €145 mn (US $170 mn) of investment to progress towards EU BAT technologies at all seven of its existing viscose fibre production plants, which are located in India, Indonesia, China and Thailand.
Limited public disclosure, including information on reduction of certain emissions within a set timeframe on a group/facility level, but no systematic reporting of progress made by all facilities in relation to EU BAT parameters.
ABG communicated that each of their site has a grievance management policy used to address the grievances of the community. The access to policy and grievance mechanism publicly available,7 but not available in local languages (only grievance forms in local languages). Incidents/complaints not publicly accessible, registered internally.
Green shirt: 33/35 buttons
Sourcing risk of sourcing from Ancient & Endangered Forests and other Controversial Sources has been resolved.
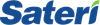
Sateri has committed to achieve EU BAT norms at all its sites by 2023.3
5 out of 5 viscose producing facilities; Sateri Fujian, Sateri Jiujiang and Sateri Jiangxi, Sateri China, and Sateri Jiangsu.
n/a
n/a
Sateri communicated that it has a central grievance mechanism and an environmental complaints handling procedure at all operation sites. The access to designated email is accessible on the website in English and Chinese.8
According to Sateri, each mill has an official WeChat account where anyone can leave a message to raise complaints. Incidents/complaints not publicly accessible.
Red/yellow shirt: 13/35 buttons
Associated with High Risk of Sourcing from Ancient & Endangered Forests and other Controversial Sources. Risk is known and no action is taken.

APR expected full compliance with EU BAT by 2023.4
0 out of 1 viscose producing facilities.
APR communicated that they are investing €14.8 mn (USD 15.7 mn) for the installation of an additional CS2/H2S recovery system to improve CS2 recovery and €68.000 (USD 80.000) in an effluent reduction project. The projects are due for completion and commissioning in Q4 of 2021 and at the end of Q4 2020, respectively.
APR communicated that any grievances are handled in accordance to the procedure and internally documented. Available on the website in English and Bahasa.9
Incidents/complaints not publicly accessible.
Red/yellow shirt: 5/35 buttons
Associated with High Risk of Sourcing from Ancient & Endangered Forests and other Controversial Sources. Risk is known and no action is taken.

No clear commitment to EU BAT. CV communicated that the CV Roadmap 2025 will be published in 2020, including basic-level requirements for members to achieve or go even beyond EU BAT by 2025.
n/a
CV communicated that Sateri and Tangshan Sanyou are aligned with EU BAT, according to STS reports.
Not disclosed.
CV communicated that it will disclose members' general investment in the field of sustainability every year, however this is not specific to investments in closed-loop technologies.
Sustainability report provides very limited disclosure on performance of CV members in line with only one or two core EU BAT parameters, and only on seven CV members. No systematic reporting of progress made by each member in relation to EU BAT parameters. Reporting is at times misleading by refering to values as core EU BAT indicators, when this is not the case. CV communicated that it cannot publicly release or disclose data on their members.
There is no grievance mechanism in place on the CV level.
n/a

n/a5
1 out of 1 viscose producing facility; ENKA’s site in Germany operates in line with emission and consumption values set out in the BREF document.
n/a
1 out of 1 viscose producing facility; ENKA’s site in Germany operates in line with emission and consumption values set out in the BREF document.
n/a
ENKA has one production site that is already operating in line with the BREF document.
ENKA discloses performance against BREF levels on their website. Data is updated annually.5
There is no grievance mechanism in place. Local complaints, inquiries and questions from individuals are directed to the regulatory authority and ENKA has to provide sufficient information and answer within a timeframe set by the authority (“Umweltinformationsgesetz”).
Green shirt: 26/35 buttons
Sourcing risk of sourcing from Ancient & Endangered Forests and other Controversial Sources has been resolved
Footnotes
Published 10 December 2020. The analysis is based on responses to a questionnaire shared with manufacturers in August 2020 and on publicly available information.
1 Lenzing Group (2020) Sustainability Targets [ONLINE] Available at: https://www.lenzing.com/sustainability/sustainability-strategy/sustainability-targets
2 Aditya Birla Group, Sustainability Report 2019 – Pulp and fibre Business [ONLINE] Available at: https://www.birlacellulose.com/policies_reports_files/policies_reports_pdf_16_1580906355.pdf
3 Sateri (2021) EU-BAT Compliance Confirmed for all Sateri Viscose Fibre Mills; Achievement Ahead of Schedule [ONLINE] Available at: https://www.sateri.com/news_events/eu-bat-compliance-confirmed-for-all-sateri-viscose-fibre-mills-achievement-ahead-of-schedule/
4 Asia Pacific Rayon (2020) Sustainability dashboard [ONLINE] Available at: https://www.aprayon.com/en/sustainability/sustainability-dashboard/responsible-operation/clean-manufacturing/
5 ENKA is a viscose filament yarn manufacturer, therefore the limits set by the EU BAT are not applicable. ENKA (n.d.) Consumption and emission data [ONLINE] Available at: http://www.enka.de/nachhaltigkeit_7_en.php.
6 Lenzing, Compliance, Express your concerns [ONLINE] Available at: https://www.lenzing.com/lenzing-group/compliance
7 Birla Cellulose (2020) Grievance Redressal Policy [ONLINE] Available at: https://www.birlacellulose.com/policies_reports_files/policies_reports_pdf_26_1600432701.pdf
8 Sateri (2020) Grievance [ONLINE] Available at: https://www.sateri.com/sustainability/grievance/
9 Asia Pacific Rayon (2020) Grievance process [ONLINE] Available at: https://www.aprayon.com/en/sustainability/grievance-process/
*Members of CV include: China Chemical Fibres Association, China Cotton Textile Association, Constant day dragon (Weifang), Funing Aoyang, Jilin Chemical Fibre, Sateri, Shandong Yamei, Shandong Yinying (Silver Hawk), Tangshan Sanyou, Xinxiang Baliu Chemical Fibre, Yibin Grace and Zhejiang Fulida, Alliance for a green development of regenerated cellulose.
Brands and producers:
Roadmap
Take a look at our roadmap towards responsible viscose for information on how you can move towards a closed loop system, too.
Consumers:
Take Action
Sign our petition or tweet your favourite retailer today to help us spread the word about viscose.
Brand categorisation
See which brands are leading the transition to responsible viscose and which are lagging behind.
Resources
We’ve made it easy for you to brush up on the need for responsible viscose by compiling our latest reports on the issue, here.
Table 1: EU BAT emissions standards for viscose staple fibre production.
Standard | Air pollution | Water pollution | Energy | Solid waste | |||
---|---|---|---|---|---|---|---|
Viscose staple fibre | EU BAT | Sulphur to air (kg/t) expressed as an average | Zinc to water (g/kg) | COD (g/t) | Sulphate (kg of SO42-/tonne) | Direct energy (GT/t) | Hazardous waste (kg/t) |
12–20 | 0.01–0.05 | 3000–5000 | 200–300 | 20–30 | 0.2–2.0 |
Source: European Commission (2007) Reference Document on Best Available Techniques in the Production of Polymers.
Table 2: Emission and consumption data for viscose filament yarn production.
Viscose filament yarn | Filament production with batch washing | Filament production with integrated washing | |
---|---|---|---|
S to air | kg | 40–60 | 170–210 |
Waste water | t | 60 | 35–130 |
SO42- to water | kg | 200–350 | 250–1000 |
Zn to water | g | 100–300 | 500–3000 |
AOX | g | 5 | 7–50 |
COD | kg | 5–6 | 6–28 |
Hazardous waste | kg | 1–5 | 1–5 |
Source: European Commission (2007) Reference Document on Best Available Techniques in the Production of Polymers.